There are many reasons for the defects of forgings, a large part of which is caused by the defects of ingot. Today, I will give you a brief description of the defects of ingot:
Segregation: The uneven distribution of chemical composition and impurities in steel ingot is called segregation. Segregation is the product of selective crystallization during solidification of molten steel. There are two kinds of segregation: dendritic segregation (or microscopic segregation) and regional segregation (or low power segregation). Dendritic segregation can be eliminated by forging and post-forging heat treatment.
2. Inclusion: non-metallic compounds in ingot that are insoluble in the base metal and cannot disappear after hot and cold treatment. There are usually silicates, sulfides and oxides. The inclusions destroy the continuity of the metal, and the stress concentration between the inclusions and the matrix metal occurs under the action of stress, and the microcracks easily occur, which inevitably reduces the mechanical properties of the forgings.
3. Gas content (purity) : hydrogen, oxygen, nitrogen and other gases are dissolved into liquid steel through the charge and furnace gas. Oxygen and nitrogen appear in the steel ingot as oxides and nitrogen compounds, while hydrogen exists in atomic state. Hydrogen is the most harmful gas in steel ingot. The solubility of hydrogen in steel decreases with the decrease of temperature, when the ingot solidification process in excess of the solubility of hydrogen is too late to precipitate from the ingot, still in the atomic state supersaturated solid dissolved in steel, then part of the diffusion into the pores of the ingot, and combined into molecules, thus forming the root cause of forging white spots. Since the vacuum treatment technology of liquid steel was adopted, the harmful gases have been basically eliminated.
4. Shrinkage cavity and porosity: shrinkage cavity is formed in the riser area, resulting in inevitable defects due to the absence of liquid steel supplement. When forging, the riser and shrinkage cavity should be removed together, otherwise the internal crack will be caused by the failure of forging shrinkage cavity. The porosity is due to the intergranular space caused by the final solidification shrinkage of the liquid steel and the microscopic pores formed by gas precipitation during the solidification process. Loose ingot structure density decreased, affecting the mechanical properties of forgings, so in forging requirements to increase the degree of deformation, in order to forge through the ingot, the loose will be eliminated.
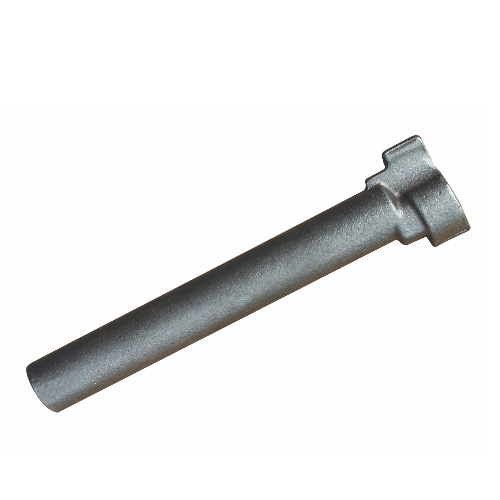